AeroBarrier: The latest in tight home envelopes
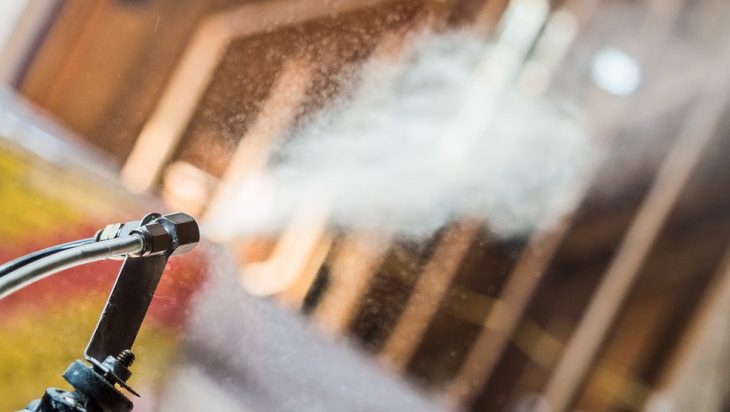
14 June 19, 2019 | by Joseph Grove, Contributing Writer
When it comes to high-performance construction techniques, there’s enough talk about envelopes that one might confuse the conversation with a trip to Office Depot or sitting through a Dave Ramsey seminar.
Two types of envelopes relate to how energy efficient a build can become. Probably better known is the building envelope. In the whole sustainability/net-zero world of energy consumption, it refers to how many apertures are allowed to exist where two surfaces meet.
Remember that homemade door at Drunk Uncle Ed’s where there were gaps large enough around it for small birds to enter? Less like an envelope. More like a sieve.
But virtually every home has those gaps. At least at Uncle Ed’s, you could see them and get out his duct tape. In most homes, however, they’re far sneakier. A couple of millimeters here. A square inch there. Add them all up, and a homeowner could have the equivalent of her backdoor open all year long—summer or winter, wet season or dry.
Even sneakier are defects in the thermal envelope. This one refers to the ability of a solid surface to keep outside temperature and humidity forces at bay and inside ones curled up at your feet like a loving spaniel.
Truth is, only recently have architects, builders and aftermarket suppliers promoted much progress in affordably and reliably keeping the home’s outdoor influences from sneaking indoors to play mischief with your energy bill and your indoor air quality.
It’s not that the professionals didn’t take the promises of improvement seriously, but among the myriad areas of improvement that came to light as environmental and legislative mandates pushed the industry toward higher performance and greater sustainability, it had other, lower-hanging fruit to pluck. Building and thermal envelopes just didn’t scream sexy the way a bank of rooftop solar panels did.
These days, builders are able to hand over keys to dwellings that are so well isolated from the environment around them that special, remedial steps must be taken to ensure the air stays fresh enough inside that occupants don’t asphyxiate on their own stale breath.
OK. That’s a stretch. But it’s not that much of a stretch.
From time to time, we’ll cover various technologies that help comprise a good building or thermal envelope. Here, we’ll look at a new product called AeroBarrier.
Spray the Loss Away
AeroBarrier is an atomized waterborne acrylic that works by infusing the atmosphere inside a partially constructed home with a specially developed sealant.
“There’s nothing like it in the market,” said Luis Imery, founder of the Imery Group, a custom home builder of Zero Energy Ready Homes , energy and building advisor, and now recently an air sealing contractor.
Currently any product involving barrier securement involves someone working for the builder to walk around the inside perimeter of the roughed home. He or she carries a caulk gun and spray foam, visually inspects for leaks and squirts them closed. This happens right before insulation is installed.
It’s like a self-guided airborne caulk,” Imery said. “You push it through the walls, and as it leaves the envelope, it’s sealing whatever crack is there, all while you control the flow of the product.”
Watch this video to learn more about AeroBarrier.
Spray-foam insulation has been around for decades and is known to work with up to 50 percent greater efficiency than traditional fiberglass products. While the central premise of AeroBarrier may bring that insulator to mind, the comparison stops at the nozzle of the applicator, which in the case of AeroBarrier is called an emitter.
The process can be described this way:
- The mobile and portable equipment is transported to the construction site by trailer. It includes a compressor, generator, blower door, emitters, hoses and the AeroBarrier machine itself, which is a computer-controlled device that monitors the application of the sealant itself.
- Emitters are set up throughout the area to be sealed to maximize the application.
- The area is prepped by taping and covering designed openings, finished flat surfaces and areas that will not be sealed, leaving exposed lines of intersection where two surfaces meet and conceivably may permit the exchange of indoor air and outdoor air.
- The space is pressurized with a blower door, which does two things. First, it measures the pre-application leakage of air. Second, it begins to set up small currents of air toward those leaks to help direct the AeroBarrier sealant.
- The AeroBarrier computer system does the rest, including controlling temperature, pressure, humidity and distribution of the sealant.
- The blower door allows the system to get real time readings, allowing the builder to dial in their desired building envelope performance
- A final blower door test verifies the sealing results. Progress and the finished results can be viewed in real time.
- Builder receives an AeroBarrier Certificate, with a pre-application and post-application leakage report, to include with the home sale.
The goal of the builder should be to build as airtight a home as possible, Imery says, much like a submarine, which when in submerged in water has zero leaks.
“You eliminate all the infiltration of outside air, and then you manage your fresh air input with controlled devices.”
The solution conjugates into the smallest holes, sealing them. The result:
- Mechanical load reduced
- Building health
- Improved comfort
- Enhanced durability
- Easy to achieve Passive House or energy code requirements
- Labor-cost reduction
- Even helps keep out bugs and rodents
AeroBarrier was developed at University of California, Davis, where it received four years of research and development. AeroBarrier is instrumental for single and multi-family projects targeting the performance requirements of LEED, ZERH, Passive House, and the 2015 IECC. The product is GREENGUARD Gold certified, meaning it contains no harmful or toxic chemicals.
Imery says one builder in Arizona is installing AeroBarrier in each home he builds, and he has made inroads in Washington and Oregon. Also a pleasant development for Imery Ratings is that since launching this spring in Georgia, 80 percent of his leads have been from individuals in the process of building their homes and only 20 percent so far from the industry.
AeroBarrier costs more than traditional sealing products, Imery says, but the cost can be netted down virtually to a net investment because as a result of applying it, the homeowner and builder can install a more affordable, more efficient HVAC system and it opens the door for the use of different insulation products. For example, if ordinarily a three-ton AC unit must be installed, the homeowner can get by with a two-ton unit, realizing right away a savings of about a thousand dollars.
The industry is taking note.
“When it comes to sealing a home, AeroBarrier is a revolutionary product,” said Geoff Ferrell, chief technology officer for Mandalay Homes. “It makes it easy to seal holes the eye and traditional construction practices miss.”
“AeroBarrier could very well be the end game in our industry’s search for a comprehensive,
cost-effective way to control leaks through building enclosures,” said Gord Cooke of Construction Instruction and Building Knowledge Canada. “Properly sealing a home or building to precise levels can be time-consuming, stressful to site staff and expensive. With ever increasing expectations of homeowners and changing building codes, homes will be expected to be more airtight than ever. There isn’t a more important technology in our industry today.”
Case Studies
Near Zero: Single Family Home
Location: Prescott Arizona
Builder: Mandalay Homes
By applying AeroBarrier Mandalay Homes transformed their typical 2,200 square foot design, from 2.0 ACH50 to .64 ACH50. This improvement in envelope air tightness reduced energy demand and made a net-zero home on a production scale financially feasible. With the improved air tightness, Mandalay is able to reduce solar requirements and add energy storage allowing them to scale its net zero design as a standard feature on all homes they build. Mandalay Homes is an eight-time recipient of the U.S. DOE Innovation Award.
Compartmentalization: Multi Family Certified Passive House
Location: New York
Builder: Synapse Development Group
At first, the units were not achieving the required air tightness required for Passive House certification. By applying AeroBarrier post manual caulking, leakage levels were reduced 47 percent. By doing so, the project achieved compartmentalization of tightness to achieve Passive House certification at .60 ACH50. All units were able to be sealed in 8 days.
Final Review
Summary
Class aptent taciti sociosqu ad litora torquent per conubia nostra, per inceptos. Lorem ipsum dolor sit amet, consectetur adipiscing elit. And finally the subconscious is the mechanism through which thought impulses which are repeated regularly with feeling and emotion are quickened, charged. And finally the subconscious is the mechanism through which thought impulses which are repeated regularly with feeling and emotion.